Nanoscope afm manual Autocad 2011 64 bit full version with crack Libc.so.6glibc 2.1064bit Trusted and high paid ptr programs How to improve the readability of a program Dark heresy adeptus astartes pdf creator Environmental health procedures 8th edition Latihan logika dan algoritma 018. Home - Santa Clara University. Bruker Multimode 8 Atomic Force Microscope Operation, Fundamentals, and Analysis Rachel A. Letteri, April 2018 4. Load sample and probe: o Remove tip/probe holder assembly (part 8) from instrument by unscrewing knob (part 15) on back-center of AFM head, and place on a table with the tip facing up (Figure 4). NanoScope™ manual. Specifically, this manual covers the following:. History and Definitions in Scanning Probe Microscopy (SPM): Section 1.0. Scanning Tunneling Microscope: Section 2.0. Contact Mode AFM: Section 3.0. TappingMode™ AFM: Section 4.0. Non-contact Mode AFM: Section 5.0. Advantages and Disadvantages of Contact.
- Application Of Different Modifiers For ...
- Nanoscope Manual
- Nanoscope Afm Manual Download
- Comprehensive Physical Studies On ...
Atomic force microscopy (AFM) is a high-resolution form of scanning probe microscopy, also known as scanning force microscopy (SFM). The instrument uses a cantilever with a sharp tip at the end to scan over the sample surface (Figure (PageIndex{1})). As the probe scans over the sample surface, attractive or repulsive forces between the tip and sample, usuually in the form of Van Der Waal forces but also can be a number of others such as electrostatic and hydrophobic/hydrophilic, cause a deflection of the cantilever. The deflection is measured by a laser (Figure (PageIndex{2})) which is reflected off the cantilever into photodiodes. As one of the photodiodes collects more light, it creates an output signal that is processed and provides information about the vertical bending of the cantilever. This data is then sent to a scanner that controls the height of the probe as it moves across the surface. The variance in height applied by the scanner can then be used to produce a three-dimensional topographical representation of the sample.
Modes of Operation
Contact Mode
The contact mode method utilizes a constant force for tip-sample interactions by maintaining a constant tip deflection (Figure (PageIndex{2}).The tip communicates the nature of the interactions that the probe is having at the surface via feedback loops and the scanner moves the entire probe in order to maintain the original deflection of the cantilever. The constant force is calculated and maintained by using Hooke's Law, ref{2}. This equation relates the force (F), spring constant (k), and cantilever deflection (x). Force constants typically range from 0.01 to 1.0 N/m. Contact mode usually has the fastest scanning times but can deform the sample surface. It is also only the only mode that can attain 'atomic resolution.'
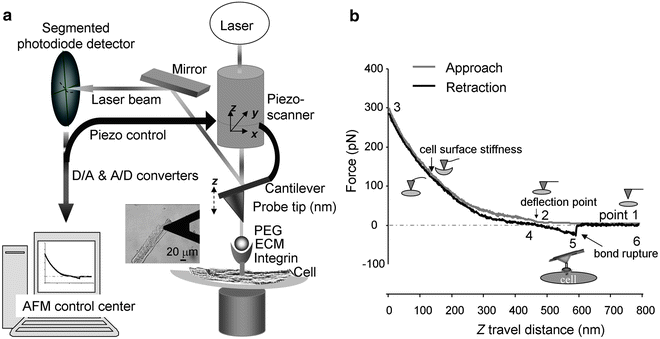
[ F = -kx label{1} ]
Tapping Mode
In the tapping mode the cantilever is externally oscillated at its fundamental resonance frequency (Figure (PageIndex{3})). A piezoelectric on top of the cantilever is used to adjust the amplitude of oscillation as the probe scans across the surface. The deviations in the oscillation frequency or amplitude due to interactions between the probe and surface are measured, and provide information about the surface or types of material present in the sample. This method is gentler than contact AFM since the tip is not dragged across the surface, but it does require longer scanning times. It also tends to provide higher lateral resolution than contact AFM.
Noncontact Mode

For noncontact mode the cantilever is oscillated just above its resonance frequency and this frequency is decreased as the tip approaches the surface and experiences the forces associated with the material (Figure (PageIndex{4})). The average tip-to-sample distance is measured as the oscillation frequency or amplitude is kept constant, which then can be used to image the surface. This method exerts very little force on the sample, which extends the lifetime of the tip. However, it usually does not provide very good resolution unless placed under a strong vacuum.
Experimental Limitations
A common problem seen in AFM images is the presence of artifacts which are distortions of the actual topography, usually either due to issues with the probe, scanner, or image processing. The AFM scans slowly which makes it more susceptible to external temperature fluctuations leading to thermal drift. This leads to artifacts and inaccurate distances between topographical features.
It is also important to consider that the tip is not perfectly sharp and therefore may not provide the best aspect ratio, which leads to a convolution of the true topography. This leads to features appearing too large or too small since the width of the probe cannot precisely move around the particles and holes on the surface. It is for this reason that tips with smaller radii of curvature provide better resolution in imaging. The tip can also produce false images and poorly contrasted images if it is blunt or broken.
The movement of particles on the surface due to the movement of the cantilever can cause noise, which forms streaks or bands in the image. Artifacts can also be made by the tip being of inadequate proportions compared to the surface being scanned. It is for this reason that it is important to use the ideal probe for the particular application.
Sample Size and Preparation
The sample size varies with the instrument but a typical size is 8 mm by 8 mm with a typical height of 1 mm. Solid samples present a problem for AFM since the tip can shift the material as it scans the surface. Solutions or dispersions are best for applying as uniform of a layer of material as possible in order to get the most accurate value of particles’ heights. This is usually done by spin-coating the solution onto freshly cleaved mica which allows the particles to stick to the surface once it has dried.
Applications of AFM
AFM is particularly versatile in its applications since it can be used in ambient temperatures and many different environments. It can be used in many different areas to analyze different kinds of samples such as semiconductors, polymers, nanoparticles, biotechnology, and cells amongst others. The most common application of AFM is for morphological studies in order to attain an understanding of the topography of the sample. Since it is common for the material to be in solution, AFM can also give the user an idea of the ability of the material to be dispersed as well as the homogeneity of the particles within that dispersion. It also can provide a lot of information about the particles being studied such as particle size, surface area, electrical properties, and chemical composition. Certain tips are capable of determining the principal mechanical, magnetic, and electrical properties of the material. For example, in magnetic force microscopy (MFM) the probe has a magnetic coating that senses magnetic, electrostatic, and atomic interactions with the surface. This type of scanning can be performed in static or dynamic mode and depicts the magnetic structure of the surface.
AFM of Carbon Nanotubes
Atomic force microscopy is usually used to study the topographical morphology of these materials. By measuring the thickness of the material it is possible to determine if bundling occurred and to what degree. Other dimensions of the sample can also be measured such as the length and width of the tubes or bundles. It is also possible to detect impurities, functional groups (Figure (PageIndex{5})), or remaining catalyst by studying the images. Various methods of producing nanotubes have been found and each demonstrates a slightly different profile of homogeneity and purity. These impurities can be carbon coated metal, amorphous carbon, or other allotropes of carbon such as fullerenes and graphite. These facts can be utilized to compare the purity and homogeneity of the samples made from different processes, as well as monitor these characteristics as different steps or reactions are performed on the material. The distance between the tip and the surface has proven itself to be an important parameter in noncontact mode AFM and has shown that if the tip is moved past the threshold distance, approximately 30 μm, it can move or damage the nanotubes. If this occurs, a useful characterization cannot be performed due to these distortions of the image.
AFM of Fullerenes
Atomic force microscopy is best applied to aggregates of fullerenes rather than individual ones. While the AFM can accurately perform height analysis of individual fullerene molecules, it has poor lateral resolution and it is difficult to accurately depict the width of an individual molecule. Another common issue that arises with contact AFM and fullerene deposited films is that the tip shifts clusters of fullerenes which can lead to discontinuities in sample images.
A Practical Guide to Using the Nanoscope Atomic Force Microscopy
The following is intended as a guide for use of the Nanoscope AFM system within the Shared Equipment Authority at Rice University (http://sea.rice.edu/). However, it can be adapted for similar AFM instruments.
Please familiarize yourself with the Figures. All relevant parts of the AFM setup are shown.
Initial Setup
Sign in.
Turn on each component shown in Figure (PageIndex{6}).
- The controller that powers the scope (the switch is at the back of the box)
- The camera monitor
- The white light source
Select imaging mode using the mode selector switch is located on the left hand side of the atomic force microscope (AFM) base (Figure (PageIndex{7}), there are three modes:
- Scanning tunneling microscopy (STM)
- Atomic force microscopy/lateral force microscopy (AFM/LFM)
- Tapping mode atomic force microscopy (TM-AFM)
Sample Preparation
Most particulate samples are imaged by immobilizing them onto mica sheet, which is fixed to a metal puck (Figure (PageIndex{6})). Samples that are in a solvent are easily deposited. To make a sample holder a sheet of Mica is punched out and stuck to double-sided carbon tape on a metal puck. In order to ensure a pristine surface, the mica sheet is cleaved by removing the top sheet with Scotch™ tape to reveal a pristine layer underneath. The sample can be spin coated onto the mica or air dried.
The spin coat method;
- Use double-sided carbon sticky tape to secure the puck on the spin coater.
- Load the sample by drop casting the sample solution onto the mica surface.
- The sample must be dry to ensure that the tip remains clean.
Puck Mounting
- Place the sample puck in the magnetic sample holder, and center the sample.
- Verify that the AFM head is sufficiently raised to clear the sample with the probe. The sample plane is lower than the plane defined by the three balls. The sample should sit below the nubs. Use the lever on the right side of the J-scanner to adjust the height. (N.B. the labels up and down refer to the tip. “Tip up” moves the sample holder down to safety, and tip down moves the sample up. Use caution when moving the sample up.)
- Select the appropriate cantilever for the desired imaging mode. The tips are fragile and expensive (ca.$20 per tip) so handle with care.
- Contact AFM use a silicon nitride tip (NP).
- Tapping AFM use a silicon tip (TESP).
Tip Mounting and Alignment
- Mount a tip using the appropriate fine tweezers. Use the tweezers carefully to avoid possible misalignment. Work on a white surface (a piece of paper or a paper towel) so that the cantilever can be easily seen. The delicate part of the tip the cantilever is located at the beveled end and should not be handled at that end (shown in Figure (PageIndex{8})). The tips are stored on a tacky gel tape. Use care, as dropping the tip will break the cantilever. Think carefully about how you approach the tip with the tweezers. Generally gripping it from the side is the best option. Once the tip is being held by the tweezers it needs to be placed in the tip holder clamp. With one hand holding the tweezers, use the other hand to open the clip by pressing down on the whole holder while it is lying on a flat hard surface. Once the clip is raised by downward pressure insert the tip (Figure (PageIndex{9})a). Make sure the tip is seated firmly and that the back end is in contact with the end of the probe groove, there is a circular hole in the clamp. When the clamp holds the tip the hole should look like a half moon, with half filled with the back straight end of the tip. The groove is larger than the tip, so try to put the tip in the same place each time you replace it to improve reproducibility.
- Carefully place the tip holder onto the three nubs to gently hold it in place. Bring the holder in at angle to avoid scraping it against the sample (Figure (PageIndex{9}) b).
- Tighten the clamping screw located on the back of the AFM head to secure the cantilever holder and to guarantee electrical contact. The screw is on the back of the laser head, at the center.
- Find the cantilever on the video display. Move the translational stage to find it.
- Adjust the focusing knob of the optical microscope (located above AFM head) to focus on the cantilever tip. Tightening the focus knob moves the camera up. Focus on the dark blob on the right hand side of the screen as that is the cantilever.
- Focus on the top mica surface, being careful not to focus on the bottom surface between the top of the double-sided carbon tape and the mica surface. Generally you will see a bubble trapped between the carbon tape and the mica surface. If you are focused on the top surface you can frequently see the reflection of the tip on the mica surface. The real focus is half way between the two cantilever focus points.
- Slowly lower the tip down to the surface, if the camera is focused properly onto the surface the cantilever tip will gradually come into view. Keep lowering until the two tips images converge into one. Please note that you can crash the tip into the surface if you go past this point. This is damaging to the tip and may not be possible to obtain an image if it happens, and the tip may have to be replaced. You will know if this happens when looking at the cantilever tip if it goes from black to bright white. At this point the tip is in contact with the surface and turns white as it is not reflecting light back into the photo-diode , but instead into the camera.
- Find the laser spot, it the spot is not visible on the camera screen look at the cantilever holder and see if it was visible. It helps to lower the brightness of the white light, use the translational stage again to search for it.
- Once the laser spot has been located use the X and Y laser adjustment knobs to align the laser spot roughly onto the tip of the cantilever.
- Maximize the sum signal using the photo-detector mirror lever located on the back of the head and the laser X and Y translation. As long as the sum signal value is above 3.6 V, the instrument will work, but keep adjusting the X and Y directions of the laser until the sum signal is as high as possible.
- To ensure that the laser is centered on the photodiode, zero the detector signals using the mirror adjustment knobs located on the top and back of the head. The knob on the top of the head adjusts TMAFM mode, and the knob at the rear of the head adjusts AFM/LFM mode. The range is -9.9 V to 9.9 V in both modes. The number will change slowly at the extremes of the range and quickly around 0 V. Ideally, the zeroed signal should be between ±0.1 V. Do this first in TMAFM mode, then switch to AFM/LFM mode and try to zero the detector. Flip back and forth between the two modes a few times (adjusting each time) until the value in both modes is as close to 0 V as possible. It will fluctuate during the experiment. If there is steady drift, you can adjust it during the experiment. If the number won’t settle down, the laser could be at a bad position on the cantilever. Move the laser spot and repeat (Figure (PageIndex{10})). Always end this step in TMAFM mode.
- Focus again on the sample surface.
- The sample surface can still be moved with respect to the camera via the sample stage. In choosing a place to image nanoparticles, avoid anything that you can see on the sample surface. The scale on the screen is 18 µm per cm.
Tip Tuning
- Log onto computer.
- The software is called Nanoscope. Close the version dialog box. Typically the screen on the left will allow adjustment of software parameters, and the screen on the right will show the data.
- On the adjustment screen, the two icons are to adjust the microscope (a picture of a microscope) and to perform data analysis (a picture of a rainbow). Click the microscope icon.
- Under the microscope pull down menu, choose profile and select tapping AFM. Don’t use another users profile. Use the “tapping” AFM.
- Before beginning tapping mode, the cantilever must be tuned to ensure correct operation. Each tip has its own resonance frequency. The cantilever can be blindly auto-tuned or manually tuned. However the auto-tuning scheme can drive the amplitude so high as to damage the tip.
Auto Tuning
- Click on the cantilever tune icon.
- Click the auto-tune button. The computer will enter the tuning procedure, automatically entering such parameters as set point and drive amplitude. If tuned correctly, the drive frequency will be approximately 300 Hz.
Manually Tuning
- Click on the cantilever tune icon.
- Select manual tuning under the sweep controls menu.
- The plot is of amplitude (white) and phase (yellow) versus frequency. The sweep width is the X-range. The central frequency is the driving frequency which should be between 270-310 Hz. Typically the initial plot will not show any peaks, and the X and Y settings will need to be adjusted in order to see the resonance plot.
- Widen the spectral window to about 100 Hz. The 270 – 310 Hz window where the driving frequency will be set needs to be visible.
- To zoom in use the green line (this software is not click and drag!):
- Left click separation
- Left click position
- Right click to do something
- Right click to clear lines
- If a peak is clipped, change the drive amplitude. Ideally this will be between 15 and 20 mV, and should be below 500 mV. If a white line is not visible (there should be a white line along the bottom of the graph), the drive amplitude must be increased.
- Ideally the peak will have a regular shape and only small shoulders. If there is a lot of noise, re-install the tip and things could improve. (Be careful as the auto-tuning scheme can drive the amplitude so high as to damage the tip.)
- At this point, auto-tuning is okay. We can see that the parameters are reasonable. To continue the manual process, continue following these steps.
- Adjust the drive amplitude so that the peak is at 2.0 V.
- Amplitude set point while tuning corresponds to the vertical off set. If it is set to 0, the green line is 0.
- Position the drive frequency not at the center of the peak, but instead at 5% toward the low energy (left) of the peak value. This offset is about 4/10th of a division. Right click three times to execute this change. This accounts for the damping that occurs when the tip approaches the sample surface.
- Left monitor - channel 2 dialogue box - click zero phase.
Image Acquisition
- Click the eyeball icon for image mode.
- Parameter adjustments.
- Other controls.
- Microscope mode: tapping.
- Z-limit max height: 5.064 µm. This can be reduced if limited in Z-resolution.
- Color table: 2.
- Engage set point: 1.00.
- Serial number of this scanner (double check since this has the factory parameter and is different from the other AFM).
- Parameter update retract; disabled.
- Scan Controls
- Scan size: 2 µm. Be careful when changing this value – it will automatically go between µm and nm
- (reasonable values are from 200 nm to 100 µm).
- Aspect ratio: 1 to 1.
- X and Y offset: 0.
- Scan angle (like scan rotation): raster on the diagonal.
- Scan rate: 1.97 Hz is fast, and 100 Hz is slow.
- Feedback Control:
- SPM: amplitude.
- Integral gain: 0.5 (this parameter and the next parameter may be changed to improve image).
- Proportional gain: 0.7.
- Amplitude set point: 1 V.
- Drive frequency: from tuning.
- Drive amplitude: from tuning.
Once all parameters are set, click engage (icon with green arrow down) to start engaging cantilever to sample surface and to begin image acquisition. The bottom of the screen should be “tip secured”. When the tip reaches the surface it automatically begins imaging.
If the amplitude set point is high, the cantilever moves far away from the surface, since the oscillation is damped as it approaches. While in free oscillation (set amplitude set point to 3), adjust drive amplitude so that the output voltage (seen on the scope) is 2 V. Big changes in this value while an experiment is running indicate that something is on the tip. Once the output voltage is at 2 V, bring the amplitude set point back down to a value that puts the z outer position line white and in the center of the bar on the software (1 V is very close).

Select channel 1 data type – height. Select channel 2 data type - amplitude. Amplitude looks like a 3D image and is an excellent visualization tool or for a presentation. However the real data is the height data.
Bring the tip down (begin with amplitude set point to 2). The goal is to tap hard enough to get a good image, but not so hard as to damage the surface of the tip. Set to 3 clicks bellow jus touching by further lowering amplitude set point with 3 left arrow clicks on the keyboard. The tip Z-center position scale on the right hand screen shows the extension on the piezo scanner. When the tip is properly adjusted, expect this value to be near the center.

Select view/scope mode (the scope icon). Check to see if trace and retrace are tracking each other. If so, the lines should look the same, but they probably will not overlap each other vertically or horizontally. If they are tracking well, then your tip is scanning the sample surface and you may return to view/image mode (the image icon). If they are not tracking well, adjust the scan rate, gains, and/or set point to improve the tracking. If tracing and retrace look completely different, you may need to decrease the set point to improve the tracking. If trace and retrace look completely different, you may need to decrease the set point one or two clicks with the left arrow key until they start having common features in both directions. Then reduce the scan rate: a reasonable value for scan sizes of 1-3 µm would be 2 Hz. Next try increasing the integral gain. As you increase the integral gain, the tracking should improve, although you will reach a value beyond which the noise will increase as the feedback loop starts to oscillate. If this happens, reduce gains, if trace and retrace still do not track satisfactorily, reduce the set point again. Once the tip is tracking the surface, choose view/image mode.
Integral gain controls the amount of integrated error signal used in the feedback calculation. The higher this parameter is set, the better the tip will track the same topography. However, if it is set too high, noise due to feedback oscillation will be introduced into the scan.
Proportional gain controls the amount of proportional arrow signal used in the feedback calculation.
Once amplitude set point is adjusted with the phase data, change channel 2 to amplitude. The data scale can be changed (it is the same as for display as it does not affect the data). In the amplitude image, lowering the voltage increases the contrast.
Move small amounts on the image surface with X and Y offset to avoid large, uninteresting objects. For example, setting the Y offset to -2 will remove features at the bottom of the image, thus shifting the image up. Changing it to -3 will then move the image one more unit up. Make sure you are using µm and not nm if you expect to see a real change.
To move further, disengage the tip (click the red up arrow icon so that the tip moves up 25 µm and secures). Move upper translational stage to keep the tip in view in the light camera. Re-engage the tip.
If the shadow in the image is drawn out, the amplitude set point should be lowered even further. The area on the image that is being drawn is controlled by the frame pull-down menu (and the up and down arrows). Lower the set point and redraw the same neighborhood to see if there is improvement. The proportional and integral gain can also be adjusted.
The frame window allows you to restart from the top, bottom, or a particular line.
Another way to adjust the amplitude set point value is to click on signal scope to ensure trace and retrace overlap. To stop Y rastering, slow scan axis.
To take a better image, increase the number of lines (512 is max), decrease the speed (1 Hz), and lower the amplitude set point. The resolution is about 10 nm in the X and Y directions due to the size of the tip. The resolution in the Z direction is less than 1 nm.
Changing the scan size allows us to zoom in on features. You can zoom in on a center point by using zoom in box (left clicking to toggle between box position and size), or you can manually enter a scan size on the left hand screen.
Click on capture (the camera icon) to grab images. To speed things up, restart the scan at an edge to grab a new image after making any changes in the scan and feedback parameters. When parameters are changed, the capture option will toggle to “ next”. There is a forced capture option, which allows you to collect an image even if parameters have been switched during the capture. It is not completely reliable.
To change the file name, select capture filename under the capture menu. The file will be saved in the!directory which is d:capture. To save the picture, under the utility pull-down menu select TIFF export. The zip drive is G:.
Image Acquisition
Analysis involves flattening the image and measuring various particle dimensions, click the spectrum button.
Select the height data (image pull-down menu, select left or right image). The new icons in the “analysis” menu are:
- Thumbnails
- Top view
- Side view
- Section analysis
- Roughness
- Rolling pin (flattening)
- Plane auto-fit
To remove the bands (striping) in the image, select the rolling pin. The order of flattening is the order of the baseline correction. A raw offset is 0 order, a straight sloping line is order 1. Typically a second order correction is chosen to remove “scanner bow” which are the dark troughs on the image plane.
To remove more shadows, draw exclusion boxes over large objects and then re-flatten. Be sure to save the file under a new name. The default is t overwrite it.
In section analysis, use the multiple cursor option to measure a particle in all dimensions. Select fixed cursor. You can save pictures of this information, but things must be written down! There is also a particle analysis menu.
Disengage the cantilever and make sure that the cantilever is in secure mode before you move the cantilever to the other spots or change to another sample.
Loosen the clamp to remove the tip and holder.
Remove the tip and replace it onto the gel sticky tape using the fine tweezers.
Recover the sample with tweezers.
Close the program.
Log out of the instrument.
After the experiment, turn off the monitor and the power of the light source. Leave the controller on.
Sign out in the log book.
AFM - Scanning Probe Microscopy
Atomic force microscopy (AFM) has become a powerful tool to investigate 2D materials and the related 2D materials (e.g., graphene) for both the nano-scale imaging as well as the measurement and analysis of the frictional properties.
The basic structure and function of the typical Nanoscope AFM system is discussed in the section on the practical guide.
For the contact mode of AFM, a schematic is shown in Figure (PageIndex{11}) The tip scans at the surface of the sample, the cantilever will have a shift of Δz, which is a function of the position of the tip. If we know the mechanical constant of the tip C, the interaction force, or the normal load of between the tip and sample can be calculated by ref{2}, where C is determined by the material and intrinsic properties of the tip and cantilever. As shown in Figure (PageIndex{11}) a, we usually treat the back side of the cantilever as a mirror to reflect the laser, so the change of the position will change the path length of the laser, and then detected by the quadrant detector.
[ F = C cdot Delta z label{2} ]
We can get the topography, height profile, phase and lateral force channel while measuring through the contact mode AFM. Comparing the tapping mode, the lateral force, also known as the friction, appears very crucial. The direct signal acquired is the current change caused due to the lateral force on the sample interacting with the tip, so the unit is usually nA. To calculate the real friction force in Newton (N) or nano-Newton (nN), you need to let this current signal time a friction coefficient, which is also determined by the intrinsic properties of the materials that makes the tip.
A typical AFM is shown in Figure (PageIndex{11}) b. The sample stage is at the inside of the bottom chamber. You can blow the gas into the chamber or pump the vacuum in need for the testing under different ambient. That is especially important in testing the frictional properties of materials.
Application Of Different Modifiers For ...
For the sample preparation part, the sample fixed on the mica mentioned earlier in the guide is for the synthesized chemical powders. For graphene, it can be simply placed on any flat substrate, such as mica, SiC, sapphire, silica, etc. Just placing the solid state sample on substrate onto the sample stage and the further work can be conducted.
Data Collection
For data collection, the topography and height profile are acquired using the same method in the tapping mode. However, there are two additional pieces of information that are necessary in order to determine the frictional properties of the material. First, the normal load. The normal load is described in ref{2}; however, what we directly get here proportional to the normal load is the setpoint we give it for the tip to the sample. It is a current. So we need a vertical force coefficient (CVF) to get what the normal load we apply to the material, as illustrated in ref{3}
[ F = I_{setpoint} cdot C_{VF} label{3} ]
For data collection, the topography and height profile are acquired using the same method in the tapping mode. However, there are two additional pieces of information that are necessary in order to determine the frictional properties of the material. First, the normal load. The normal load is described in ref{4}, where K is the stiffness of the tip, it can be get through the vibrational model of the cantilever, and usually we can get it if we buy the commercial AFM tip. L is the optical coefficient of the cantilever, it can be acquired by calibrate the force-displacement curve of the tip, as shown in Figure (PageIndex{12}). Then L can be acquired by getting the slope of process 1 or 6 in Figure (PageIndex{13}).
[ C_{VP} = frac{K}{L} label{4} ]
Figure (PageIndex{13}) is a typical friction image, it is composed of n*n lines by scanning. Each point is the friction force value corresponding to that point. All we need to do is to get the average friction for the area we are interested in. Then use this current signal multiplied by the lateral force coefficient then we can obtain the actual friction force.
During the process of collecting the original data of the lateral force (friction), for every line in the image, the friction information is actually composed of two data line: trace and retrace (see Figure (PageIndex{13})). The average of results for trace (Figure (PageIndex{13}), black line) and retrace (Figure (PageIndex{13}), red line) as the friction signal of the certain point on the line. That is to say, the actual friction is determined from ref{5}, where the Iforward and Ibackward are data points we can derive from the trace and retrace from the friction image, and CLF is the lateral force coefficient.
[ F_{f} = frac{I_{forward} - I_{backward}}{2} cdot C_{LF} label{5} ]
Data Analysis
There are several ways to compare the details of the frictional properties at the nanoscale. Figure (PageIndex{14}) is an example comparing the friction on the sample (in this case, few-layer graphene) and the friction on the substrate (SiO2). As illustrated in ref{5}, qualitatively we can easily see the friction on the graphene is way smaller than it on the SiO2 substrate. As graphene is a great lubricant and have low friction, the original data just enable us to confirm that.
Figure (PageIndex{15}) shows multi-layers of graphene on a mica. By selecting a certain cross section line and comparing both height profile and friction profile, it will provide us some information of the friction related to the structure behind this section. The friction-distance curve is a typical important path for the data analysis.
We can also take the average of friction signal for an area and compare that from the region to the region. Figure (PageIndex{16}) shows a region of the graphene with the layer numbers from 1-4. Figure (PageIndex{16}) a and b are also the topography and the friction image respectively. By compare the average friction from the area to the area, we can obviously see the friction on graphene decreases as the number of layers increases. Though Figure (PageIndex{16}) c and d we can obviously see this average friction change on the surface from 1 to 4 layers of graphene. But for a more general statistical way, getting the normalized signal of the average friction and comparing them can be more straightforward.
Another way to compare the frictional properties is that, to apply different normal load and see how the friction change, then get the information on friction-normal load curve. This is important because we know too much normal load for the materials can easily break or wear the materials. Examples and details will be discussed below.
The effect of H2O: a cautionary tale
During the process of using tip approach to graphene and applying the normal load (increasing normal load, loading process) and withdrawing the tip gradually (decreasing normal load, unloading process), the friction on graphene exhibits hysteresis, which means a large increment of the friction while we drag off the tip. This process can be analyzed from friction-normal load curve, as shown in Figure (PageIndex{17}). It was thought that this effect may be due to the detail of interacting behavior of the contact area between the tip and graphene. However, if you test this in different ambient conditions, for example if nitrogen was blown into the chamber while testing occured, this hysteresis disappears.
Figure (PageIndex{17}) Friction hysteresis on the surface of graphene/Cu. Adapted from P. Egberts, G. H. Han, X. Z. Liu, A. T. C. Johnson, and R. W. Carpick, ACS Nano, 2014, 8, 5012. Copyright: American Chemical Society (2014).
In order to explore the mechanism of such a phenomenon, a series of friction test under different conditions. A key factor here is the humidity in the testing environment. Figure (PageIndex{18}) is a typical friction measurement on monolayer and 3-layer graphene on SiOx. We can see the friction hysteresis is very different under dry nitrogen gas (0.1% humidity) and the ambient (24% humidity) from Figure (PageIndex{19}).
Simulation on this system suggests this friction hysteresis on the surface of graphene is due to the water interacting with the surface of graphene. The contact angle between the tip/water molecule-graphene interfaces is the key component. The further study suggests once you put the graphene samples in air and expose them for a long period of times (several days), the chemical bonding at the surface can change due to the water molecule in the air so that the friction properties at nanoscale can be very different.
Nanoscope Manual
The bond between the material under investigation and the substrate can be very vital for the friction behavior at the nanoscale. The studies during the years suggest that the friction of the graphene will decrease as the number of layers increase. This is adaptable for suspended graphene (with nothing to support it), and graphene on most of substrates (such as SiOx, Cu foil and so on). However, if the graphene is supported by fresh cleaved mica surface, there’s no difference for the frictional properties of different-layer graphene, this is due to the large surface dissipation energy, so the graphene is very firmly fixed to the mica.
However, on the other hand, the surface of mica is also hydrophilic, this is causal to the water distribution on the surface of mica, and the water intercalation between the graphene and mica bonding. Through the friction measurement of the graphene on mica, we can analyze this system quantitatively, as shown in Figure (PageIndex{18}).
Summary
This case study just gives an example that, contact-mode Atomic Force Microscopy, or Frictional Force Microscopy is a powerful tool to investigate the frictional properties of materials, for the use both in scientific research as well as chemical industry.
The most important lesson for researchers is that in analyzing any literature data it is important to know what the relative humidity conditions are for the particular experiment, such that various experiments may be compared directly.
A Veeco (formerly Digital Instruments) Nanoscope III was installed in September 2005.
This instrument is capable of tapping and contact-mode atomic force microscopy (AFM), scanning tunneling microscopy (STM), magnetic force microscopy, and force-modulation microscopy.
Nanoscope Afm Manual Download
In addition, it has a multimode heater and cooler for in-situ studies.
Instrument Specifications
Comprehensive Physical Studies On ...
Scanner Range (XxYxZ)
| Modes
|
Noise
| |
Sample Size
| Accessories
|
Vibrational and Acoustic Isolation
|